A fabless company is a manufacturer that works with and consigns production to outside companies.
Efforts toward higher safety and security
The Process from Product Development to Sales
DyDo DRINCO is a fabless company that works with other companies to manufacture and distribute vending machines and products. The company performs thorough quality checks in-house, as well as rigorous quality checks at subcontractors' plants.
At DyDo DRINCO, we will continue to maintain a dependable quality assurance and management system to deliver products and services to our customers that offer safety and reliability.
What is a fabless company?
-
Product Development
- ・Safety checks of product designs and ingredients
- ・Checks of packaging materials and labeling
-
Ingredients Procurement
- ・Quality checks
- ・Acceptance inspections
- ・Visits to points of origin as necessary
-
Production and Shipping
- ・Production management and product inspections based on internal quality control regulations
- ・Double checking internally and by partner companies to ensure proper release decision
-
Distribution and Sales
- ・Thorough freshness management
- ・Thorough management of storage environment
- ・Thorough product and sales management
-
Customer
- ・In-house sharing of customer feedback
- ・Appropriate information disclosure to customers
Thorough Checks of Ingredient Specifications and Quality
As a fabless company, DyDo DRINCO subcontracts mass production to external plants, while product concepts, recipes, and other planning and development tasks are conducted in-house. To ensure the products that reach our customers are safe and reliable in addition to being tasty, we prioritize maintaining a dependable quality assurance and management framework. Starting at the phase of product planning, we apply attention to checking the ingredient and quality specification sheets provided by suppliers for each ingredient that will be used in a product. In addition to confirming that legal requirements are met for all ingredients and furthermore we review safety-related information such as residual agricultural chemicals or allergens.
Pre-evaluation meetings at product planning stage
- Quality Control Section
- Product Dvelopment Section
-
Check via ingredient specification sheetReview of details including ingredient manufacture, country of production, blending ratio, allergen presence, GMO presence, presence of beef- or pork-derived ingredients
-
Check via quality specification sheet (statement of quality assurance)Quality standards, manufacturing processes, handling conditions, safety according to Food Sanitation Act,* checking for the presence of residual agricultural chemicals
* The Food Sanitation Act is a Japanese law established to set standards for foodstuffs to prevent sanitation hazards resulting from ingestion of food or drink, including additives used to protect people from toxic and harmful substances or bacteria.
Visits to Production Regions and Processing Plants
We establish strict standards for ingredients at the product planning stage and then procure those ingredients only from suppliers that clear those standards. For major imported ingredients our managers visit and check in person on growing conditions of agricultural products at farms, and manufacturing processes, hygiene management, and other aspects at processing plants. We also work to assure safety and improve the quality of ingredients by communicating the results of our visits directly to our business partners.
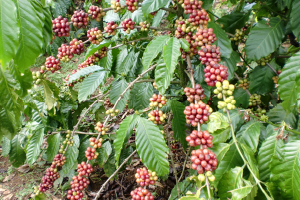
Measures Pertaining to Radioactive Substances
-
Scintillation
detector -
Germanium
semiconductor
detctor -
Testing
in progress
DyDo DRINCO uses a radioactivity measuring instrument to regularly test the safety of all products, the water used in products and domestically grown tea leaves as ingredients. For other ingredients besides tea, we use only ingredients whose safety is guaranteed.
Inspection System for Producing Coffee
Click each process for details
- ・Export
- ・Passes residual agricultural chemical test
- ・Arrival in port
- Green coffee
bean production
process - Roasting plant
-
- Farm (harvesting)
- Harvesting of ripe red coffee cherries
-
Coffee farm
-
- Drying, Hulling, Selection
- Selection by standard/grade Removal of defective beans and foreign matter (stones, wood chips, etc.)
-
- Drying
- Hulling
- Electronic sorting
-
- Quality inspection
- Visual examination
Sensory evaluation -
-
- Delivery of green coffee beans
- Acceptance inspection
Sensory evaluation
-
- Roasting
- Weight measurement
Roasting degree inspection
Sensory evaluation -
-
- Grinding
- Granularity inspeciton
Sensory evaluation -
-
- Packing and shipping
- Weight measurement
Final product inspection -
Inspection System for Producing Green Tea
Click each process for details
- Unprocessed
Tea Process - Selection /
Inspection
Process - Packing
Process
-
- Tea plantation
- Cultivation management
Growth status checking -
-
- Unprocessed tea plant
- Visual check fresh tea leaves
Moisture test
Sensory evaluation -
-
- Unprocessed tea*
- Visual examination
Sensory evaluation
Quality inspection -
-
- Selection process
- Visual examination
Sensory evaluation -
-
- Blend/Finished product inspection
- Visual examination
Sensory evaluation -
-
- Teabag filling and packing
- Visual examination
Weight check -
-
- Final product inspection
- Sensory evaluation
Quality inspection
Residual agricultural chemical test
-
- Shipping
- Visual examination
Volume check -
A Double-Check System for Products
DyDo DRINCO has established a system of double checks as a fabless company that subcontracts manufacturing to affiliate plants. We work with affiliate plants on ensuring a rigorous management and inspection system to constantly maintain safe and reliable manufacturing and distribution.
Safety and reliability are not achievable by individuals working alone. It is achieved by using an organization-wide system that emphasizes keeping safety in mind at all times and involves daily quality control efforts based on the methodologies of 5S (seiri, seiton, seiso, seiketsu, and shukan [sort, organize, clean, maintain, and discipline ]) and 5W1H (who, what, where, when, why, how).
Checks at Each Affiliate Plant
Based on quality control standards at the respective affiliate plant, various tests are conducted—tests for each process, post-manufacturing product inspection, constant temperature testing, bacteriological testing, etc.
-
Control panel
-
Monitoring panel
-
Sensory evaluation
-
Monitoring room
DyDo DRINCO Checks
Product samples and inspection check sheets from each affiliate plant are verified, amongst other measures.
-
Component analysis data screen
-
Component extractor
-
Sensory evaluation
-
Quantitatice analysis check of tannins, caffeine, etc.
-
High-speed liquid chromatography (HPLC)
Auditing of affiliate plants
- ・Audits of control points, inspection records
- ・Demand for improvement when a problem occurs
-
Affiliate plant
- Quality control Hygiene control
- Inspection records Line equipment status
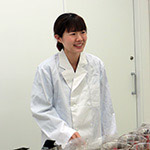
Tomoe Tagawa
Production Control Department,
DyDo DRINCO, Inc.
We always try to see things from the customer's perspective and supply products that we would recommend to our own families with confidence. Prior to a product's release we thoroughly investigate any areas of risk with regard to product labeling or ingredients to guarantee the product's safety.
We also check that no operational problems are encountered with a product at the manufacturing plant, and do not rely solely upon the plant's assessment. Before shipping, we always conduct a visual examination of the product and labeling, check the product's characteristics and physical properties, and perform a sensory evaluation to ensure there are no problems.
We aim to assure the safety of products and further improve quality from the customer's perspective so that DyDo products are liked by one and all.
Quality Assurance Audits at Affiliate Plants
DyDo DRINCO conducts annual quality assurance audits at the affiliated plants to which it outsources production. We ask plants to self-assess a quality assurance audit check sheet that features more than 150 items covering eight categories, and also send our own inspectors to conduct on-site assessment verifications. Feeding back the results of these audits, we consider solutions to issues together with affiliated plants, and in so doing seek to raise safety and quality in the production process, as well as cultivate relationships of trust.
▼Quality Assurance Audit Check Criteria
Category | Details |
---|---|
Quality assurance system |
Has a quality assurance system been built and implemented as a company? |
Plant environment and equipment |
Is the environment maintained to allow for safe and reliable product manufacturing? |
Staff management |
Is hygiene management and education carried out for production staff? |
Raw material/ingredient management |
Are appropriate methods of procurement, intake and storage applied to ingredients? |
Production process management |
Are procedures in place to allow for safe and reliable product manufacturing? |
Product warehousing and shipping |
Is rigorous storage and shipping management carried out within a safe warehouse environment? |
Quality control |
Are operations carried out based on an appropriate quality control system and environment? |
Quality assurance |
Have documents and procedures been systematized to guarantee product quality? |
Ensuring Safety and Comfort for Customers Using Our Vending Machines
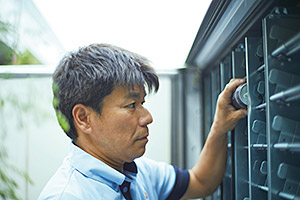
At DyDo DRINCO, we view vending machines as customer-facing "retail outlets," and work to ensure a retail environment that customers can use in comfort. Each vending machine has a team member assigned to it who is responsible for visits, resupplies, and product lineup changes, as well as collecting empty cans and bottles, and cleaning up the immediate vicinity. Through our unique system, we monitor vending machine stocking levels and conduct thoroughgoing quality control right up until the point of consumption.
Using Good Water
Water is a vital ingredient for energy drinks, as it comprises the bulk of the beverage. DAIDO Pharmaceutical's plant is located in an area with rich natural resources, and high-quality underground water is pumped up for use, and well water is purified. In the process of purifying well water, quality checks are performed three times a day using an inspection sheet devised in-house, along with other measures employed to secure and maintain the safety of water used as the base for our energy drinks.
- Good-quality Underground Water
- Well Water Treatment Equipment
- Filtering Mechanism
- Reverse Osmosis Membrane Device
- Water Purification Equipment
- Water Quality Test
- Treatment Water Tank
- Purified Water
- Quality inspections
(3 times a day)
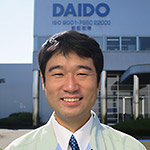
Makoto Mukoda
Production Department,
DAIDO Pharmaceutical Corporation
Among general utilities for supporting the manufacturing process, I am in charge of maintenance and management of water equipment. Awareness of water has changed in recent years, including from the perspective of food safety, and we are working hard in maintenance and management to further improve the quality of water-related equipment. For example, we periodically review and update the check items in the inspection chart used for quality inspection of processes involving water for manufacturing to ensure they are optimal. Going forward, we will continue to keep in mind that "good water is good for people," and work to provide products with higher safety that can contribute to the health and happiness of our customers. We want to continue improving, with the objective of maintaining our position as No. 1 in the industry in terms of quality as well as sales.
Food Defense Measures
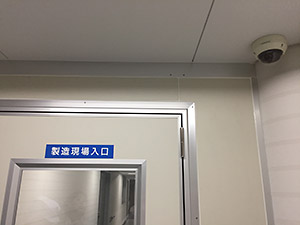
DAIDO Pharmaceutical takes food defense measures for building a safe, concern-free production system. Entry into the plant is restricted by ID card, and over 100 quality assurance cameras are set up inside and outside the plant to capture footage that can be used for analysis if trouble ever does occur in the manufacturing process. In addition to strengthening such physical measures, we have established an open and transparent workplace environment where management and team members can mix freely and engage in unfettered interaction on a daily basis.
Our Approach to Quality at Tarami
At Tarami, we consider thorough quality management to be an essential condition for delivering tasty food products to our customers. The company is certified under both the ISO 9001 international standard for quality management systems and FSSC 22000 international certification scheme for food safety systems. Moving forward, we will continue to conduct strict quality and product inspections and aim to further improve quality.
